RDF briquetting machine has a special design, including pressing
wheels, modules, anti-stifling machines and fully automatic oil
pumps, etc., which is suitable for extrusion and solidification
molding of various combustible wastes. It has a reasonable
structure, high production efficiency, low energy consumption,
strong adaptability, simple operation, reliable performance, and
easy to move. RDF briquetting machine is widely used in waste power
plants, cement plants and various industrial boilers.
RDF briquetting machine uses solid waste as raw material, and after
crushing, pressurizing, densifying and molding, it becomes a small
stick-shaped solid briquette fuel. It is an ideal equipment for
waste recycling.
Model | Pellet size(mm) | Dimension(mm) | Weight | Power | Capacity |
XRD-YK600 | 32*32*50-100 | 2800*1350*1800 | 2800kg | 55kw | 0.8-1ton/h |
XRD-YK800 | 32*32*50-100 | 3500*1900*2200 | 3800kg | 75kw | 1.5-2ton/h |
XRD-YK1000 | 32*32*50-100 | 3700*2100*2200 | 4800kg | 110kw | 2-3ton/h |
XRD-YK1200 | 32*32*50-100 | 4700*2750*2600 | 16000kg | 200kw | 4-6ton/h |
Product Application
Application scope of RDF industrial solid waste combustion
briquetting machine: various industrial solid wastes, including
shoes, clothing scraps, leather, paper mill slag, domestic garbage,
stale garbage, sludge, plastics, foam, branches and bark, crop
straw, fruit shells, sawdust, feces, etc.
In short, the application scope of RDF solid waste fuel briquetting
machine is very wide, which can be divided into industrial garbage,
domestic garbage, garden garbage, agricultural garbage, aquaculture
garbage, etc.
The fuel rods made by RDF garbage briquetting machine are suitable
for use as fuel in furnaces, boilers, and power plants. The ash
after combustion is weed ash directly used in farmland.
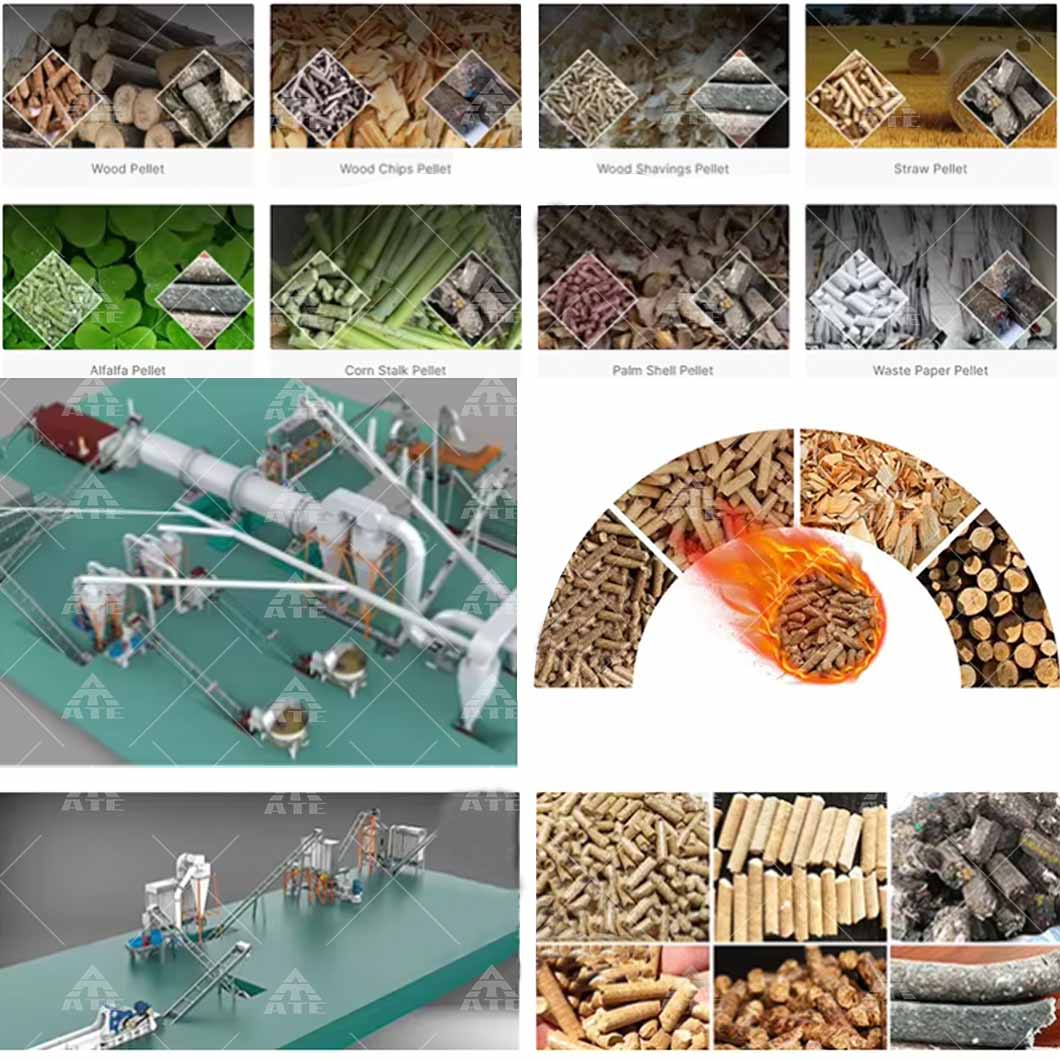
The process flow of preparing RDF (waste-derived fuel) through
resource treatment of domestic garbage, waste textiles, cloth,
leather, etc.:
1. Pretreatment and transportation
Waste textiles enter the processing line through a chain conveyor
or a belt conveyor to achieve automatic loading.
2. Coarse crushing
The material is coarsely crushed by a double-axis shredder or an
industrial waste crusher to reduce the large volume of material to
a size suitable for subsequent processing.
3. Sorting and purification
Magnetic separation: Separate ferromagnetic metal impurities and
recover metal resources.
Wind separation: Use airflow to separate light combustibles (such
as fabrics and plastics) from heavy impurities (such as sand and
gravel).
4. Fine crushing
The sorted combustibles enter the fine shredder and are further
crushed into uniform particles of 50-100mm to meet the size
requirements of RDF fuel.
5. Molding
Some processes will add RDF molding machines to compress the
crushed materials into high-density particles or fuel rods for easy
transportation and storage.
6. Finished product application
The final RDF fuel can be directly used in cement kilns, power
plants, etc. to replace coal and realize energy utilization.